내 블로그에 오신 것을 환영합니다!
본론으로 들어가기 전에, 제가 더 많은 정보를 공유하고, 커뮤니티와 소통하고, 업데이트를 게시하는 소셜 미디어 플랫폼에 함께해 주세요. 저와 소통하는 방법은 다음과 같습니다.
페이스북:https://www.facebook.com/profile.php?id=61571539990739
자, 이제 함께 여정을 시작해 볼까요? 여기 있는 내용이 통찰력 있고, 흥미롭고, 가치 있다고 느끼시기를 바랍니다.
목차
소개
Looking for tubing that perfectly fits unusual profiles or complex equipment designs? Special shaped tubes are your solution. These custom steel tubes—square, oval, D-profiled, or bespoke—offer precise fit, structural performance, and aesthetic appeal. This guide will help you explore the benefits, materials, manufacturing methods, and applications in various industries.
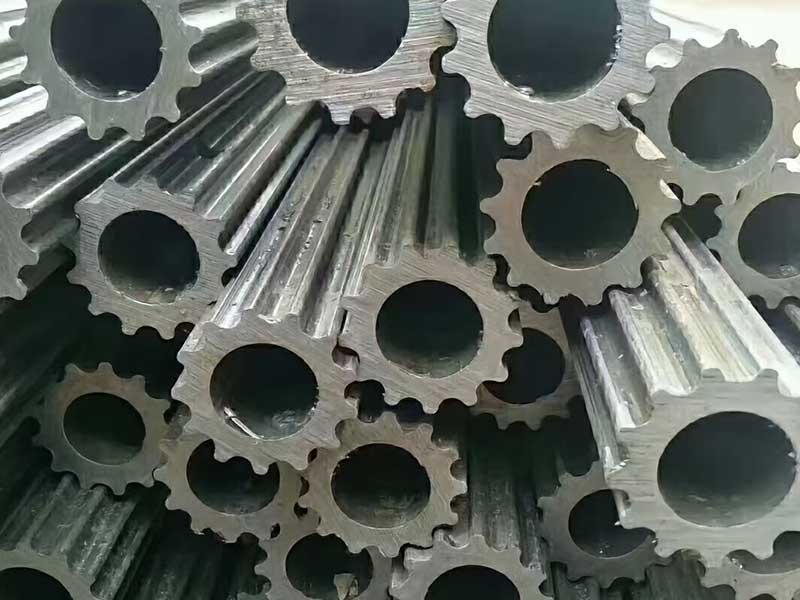
Understanding Special Shaped Tubes: Definition and Core Benefits
Special shaped tubes are hollow profiles deviating from circular cross-sections. Common shapes include square, rectangular, oval, D-shaped, triangular, or fully customized forms.
Key advantages:
- Tailored fit saves on welding and assembly work
- Consistent mechanical properties along precise geometry
- More efficient material usage for structural needs
- Easy integration for clean, seamless assemblies
According to a 2023 industry report, over 65% of manufacturers using special shaped tubes reported labor savings from reduced welding by 20%.
Materials and Manufacturing Methods for Special Shaped Tubes
Choosing the right material is essential. Options range from carbon steel, alloy steel, stainless steel, to aluminum or copper alloys. Each offers different strength, corrosion resistance, and weldability features.
Manufacturing techniques include:
- Extrusion in soft metals like aluminum
- Roll forming and welding for steel, creating consistent shapes
- Laser cutting or pressing for precision notches and slots
- Cold-drawing for tight tolerances and strong grain structure
Careful material and method selection ensures your special shaped tubes meet both performance and cost expectations.
Industry Applications and Long-Tail Use Cases
Special shaped tubes are used across diverse applications:
- Architectural frameworks (sign frames, racks)
- Automotive structural parts (chassis beams, roof supports)
- Furniture (table legs, ergonomic profiles)
- HVAC components (duct profiles, grille frames)
- Equipment tubing (instrumentation panels, safety railing)
By creating accurate prefabricated tubing for complex parts, manufacturers reduce assembly time and improve aesthetics.
Performance Comparison: Special Shaped Tubes vs Standard Pipes
특징 | Special Shaped Tubes | Round Pipes |
---|---|---|
Fit to profile | High—custom-exact | Poor—needs cutting/welding |
Assembly time | Lower—fewer joins | Higher—extensive welding |
Weight-to-strength ratio | Better—optimized geometry | Less efficient |
Aesthetics | Superior—clean finish | Industrial look |
Cost-effectiveness | Depends on complexity | Good for simple uses |
Manufacturers choosing special shaped tubes for high-precision assembly report up to 15% time savings and material efficiency gains.
Quality Control, Tolerances, and Surface Finishes
When producing special shaped tubes, tight tolerances and good finish are critical:
- Dimensional tolerances must be controlled to ±0.1 mm for automated assembly
- Straightness and flatness checks prevent misalignment in frames or machinery
- Surface finishes (polished, galvanized, powder-coated) enhance appearance and resistance to wear
Standards like EN 10305 or ASTM A500 offer yardsticks for measuring compliance, which improves both aesthetics and function.
Choosing the Right Supplier for Special Shaped Tubes
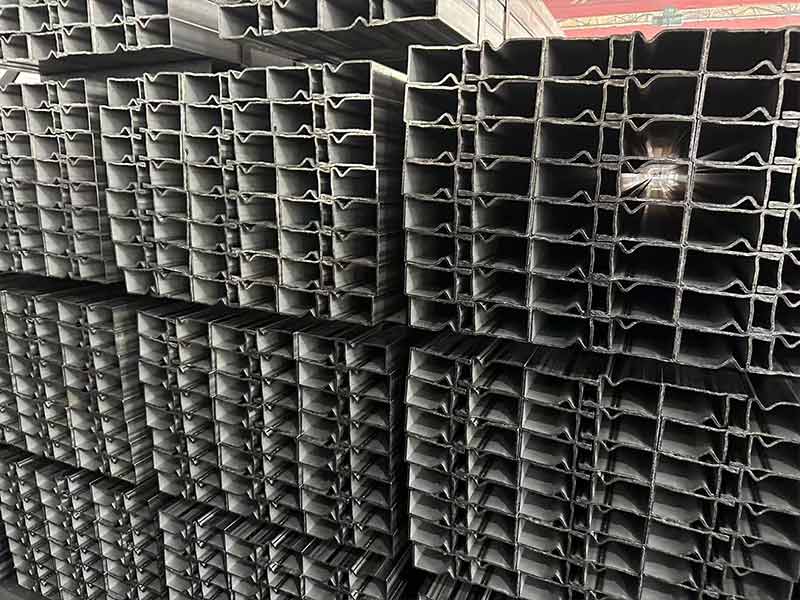
Here are essential factors:
- Wide material and shape capability
- Custom mill setup and precision tooling
- Quality certifications and testing protocols
- Flexibility in order size and turnaround
- Value-added services—cutting, bending, finishing, Kitting
A reliable supplier becomes your strategic partner, ensuring consistent quality and production support.
결론
Special shaped tubes offer unmatched utility in design, structure, and workflow efficiency. They minimize fabrication steps, improve product appearance, and enhance structural performance—all translating into long-term ROI. When you choose precision tubing, you’re investing in better builds and quicker iterations.
Ready to upgrade your tubing solutions? Contact us today to explore custom special shaped tubes tailored to your specific needs.
자주 묻는 질문
What materials can you get special shaped tubes in?
Common options include carbon steel, alloy steel, stainless steel, aluminum, and copper—all chosen based on strength, corrosion resistance, or weight needs.
How long does producing special shaped tubes take?
Standard lead times range from 2–6 weeks, depending on shape complexity and tape-cutting or bending prep required.
Can these tubes be pre-drilled or pre-finished?
Yes—many suppliers offer secondary services like hole punching, notching, laser cutting, bending, and surface coating.
Are they more expensive than round pipes?
Unit cost is higher, but savings from reduced labor, assembly time, and material waste often offset initial differences.
What shapes are available?
Everything from basic square and rectangular to oval, D-profile, triangular, or fully custom cross-sections—you name it.