Chào mừng đến với Blog của tôi!
Trước khi đi sâu vào nội dung, tôi rất muốn bạn tham gia cùng tôi trên các nền tảng truyền thông xã hội của tôi, nơi tôi chia sẻ thêm nhiều hiểu biết sâu sắc, tương tác với cộng đồng và đăng các bản cập nhật. Sau đây là cách bạn có thể kết nối với tôi:
Facebook:https://www.facebook.com/profile.php?id=61571539990739
Bây giờ, chúng ta hãy cùng nhau bắt đầu hành trình. Tôi hy vọng bạn thấy nội dung ở đây sâu sắc, hấp dẫn và có giá trị.
Mục lục
Welcome to the foundational guide on steel plate and coil, two of the most fundamental and versatile forms of steel that underpin our modern world.
Giới thiệu
Steel plate & coils are fundamental components in various industries, including construction, automotive, and manufacturing. Their versatility and strength make them indispensable in creating structures, machinery, and everyday products. This guide aims to provide beginners with a comprehensive understanding of steel plates and coils, covering their types, manufacturing processes, applications, and more.
The Fiery Genesis: How Steel Plate & Coil Are Made
From Molten Metal to Solid Slab
The process begins with the creation of steel itself. This typically happens in either a blast furnace, which uses iron ore, coke (a high-carbon fuel), and limestone, or an electric arc furnace (EAF), which primarily uses recycled steel scrap. The output is molten steel, which is then refined to achieve the desired chemical composition. Alloying elements such as carbon, manganese, and others are added to impart specific characteristics like strength, hardness, and corrosion resistance.
Once the steel is ready, it is cast into a solid, semi-finished shape. For flat-rolled products, this is a slab – a thick, rectangular block of steel that can be several feet wide and many feet long. These slabs are the raw material for the rolling mills where steel plate and coil are born.
The Magic of Hot Rolling: Shaping the Steel
Hot rolling is the most common method for producing both steel plate and coil. As the name suggests, this process involves heating the steel slab to a very high temperature, typically above its recrystallization point, which for steel is over 1,700°F (926°C). At this temperature, the steel becomes malleable and can be shaped with relative ease.
The glowing, red-hot slab is then passed through a series of massive rollers. Each pass reduces the thickness of the slab and increases its length. This is a highly controlled process, with sophisticated sensors and computer systems monitoring and adjusting the rollers to ensure the final product meets precise dimensional specifications.
For steel coil, the now-elongated and thinned steel sheet is passed through a final set of finishing rollers to achieve the desired surface finish and thickness. It is then cooled and coiled into the familiar cylindrical shape.
For steel plate, the process can be similar, with the plate being cut to length after rolling. However, for thicker plates, the process might involve a reversing mill, where the plate is passed back and forth through a single set of rollers until the desired thickness is achieved.
A key characteristic of hot-rolled steel is its slightly rougher, “scaly” surface finish, which is a result of the steel cooling from a high temperature.
The Finesse of Cold Rolling: A Refined Finish
For applications that require a smoother, more refined surface and tighter dimensional tolerances, a further step is introduced: cold rolling. Cold rolling takes a hot-rolled coil, which has been cooled and had its surface scale removed through a process called pickling (an acid bath), and passes it through another set of rollers at room temperature.
Because the steel is not heated, significantly more pressure is required to reduce its thickness. This process not only improves the surface finish but also increases the strength and hardness of the steel through a phenomenon known as work hardening. Cold-rolled steel can be up to 20% stronger than its hot-rolled counterpart.
Cold-rolled steel is typically produced in coil form and is the material of choice for applications where a high-quality surface is paramount, such as in automotive body panels, home appliances, and furniture.
A World of Variety: Navigating the Types of Tấm thép & cuộn
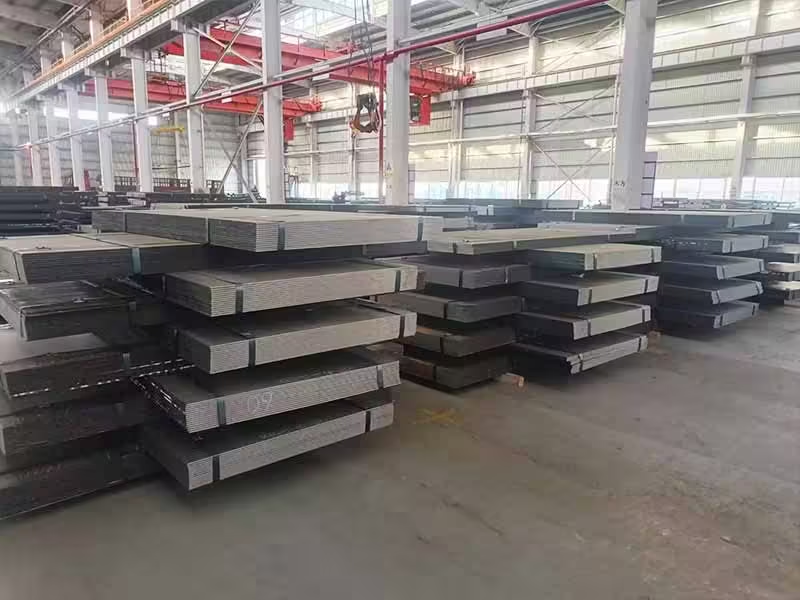
Not all steel plate and coil are created equal. The specific needs of an application dictate the type of steel used. This is where the concepts of grades and coatings come into play. The sheer number of available options can be overwhelming for a beginner, but we can group them into a few key categories to make them easier to understand.
Carbon Steel: The Workhorse of the Industry
Carbon steel is the most common type of steel and is defined by its carbon content. The amount of carbon in the steel has a direct impact on its properties.
- Low-Carbon Steel (Mild Steel): With a carbon content typically below 0.30%, this is the most widely used type of steel. It is relatively soft, ductile, and easy to weld, making it suitable for a vast range of applications, from car bodies to structural beams.
- Medium-Carbon Steel: With a carbon content ranging from 0.30% to 0.60%, this steel is stronger and harder than low-carbon steel but is less ductile. It is often used for machinery parts, axles, and gears.
- High-Carbon Steel: Containing more than 0.60% carbon, this steel is the hardest and most wear-resistant of the carbon steels. It is used for applications where durability is critical, such as in cutting tools, springs, and high-strength wires.
Alloy Steel: Enhanced Performance
Alloy steels take carbon steel a step further by incorporating other elements to enhance specific properties. These alloying elements can include manganese, nickel, chromium, molybdenum, and vanadium, among others. The addition of these elements can significantly improve a steel’s strength, toughness, corrosion resistance, and heat resistance. Alloy steel plates and coils are used in more demanding applications, such as in the aerospace industry, for pressure vessels, and in high-performance automotive components.
Stainless Steel: The Champion of Corrosion Resistance
Stainless steel is renowned for its exceptional resistance to rust and corrosion. This property is achieved by adding a significant amount of chromium (typically a minimum of 10.5%) to the steel. The chromium forms a passive, self-healing oxide layer on the surface of the steel that protects it from the environment.
There are many different grades of stainless steel, each with its own unique combination of properties. They are widely used in applications where hygiene and corrosion resistance are paramount, such as in food processing equipment, medical instruments, and architectural cladding.
Coated Steel: A Protective Layer
To further enhance the durability and longevity of steel plate and coil, various coatings can be applied to the surface. These coatings provide a barrier against corrosion and can also improve the aesthetic appeal of the final product.
- Galvanized Steel: This involves coating the steel with a layer of zinc. The zinc provides excellent corrosion protection, even if the surface is scratched. Galvanized steel is commonly used for roofing, ductwork, and outdoor structures.
- Aluminized Steel: In this process, the steel is coated with an aluminum-silicon alloy. This provides excellent heat resistance and is often used for exhaust systems and industrial ovens.
- Pre-painted Steel: Steel coils can be painted in a continuous process before they are fabricated into final products. This offers a wide range of colors and finishes and is commonly used for metal buildings, garage doors, and appliances.
Steel Plate vs. Steel Coil: A Head-to-Head Comparison
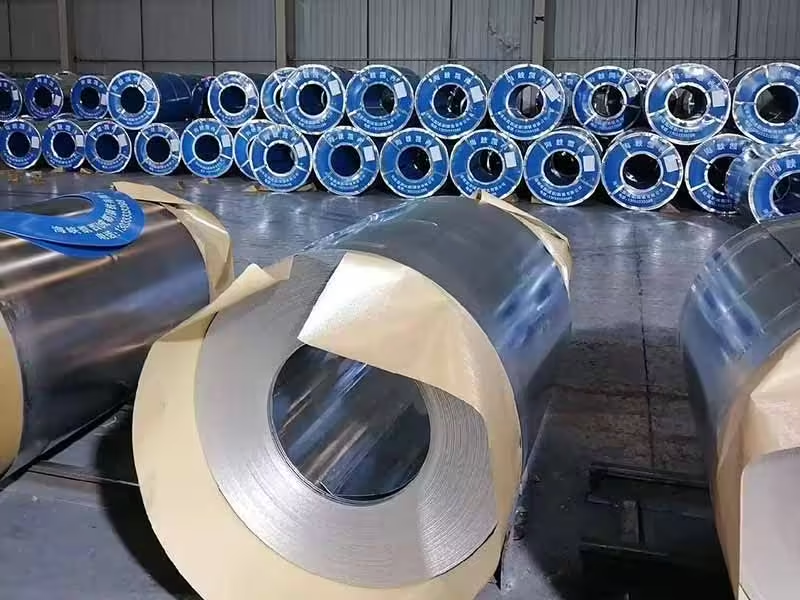
To help you better understand the key differences and typical applications of these two fundamental steel products, here is a comparative table:
Tính năng | Tấm thép | Cuộn thép |
---|---|---|
Form | Flat, discrete sheets of a defined length and width. | A continuous sheet of steel wound into a cylindrical roll. |
Typical Thickness | Generally thicker, often 6mm (approximately 1/4 inch) and above. | Typically thinner, with thicknesses ranging from less than a millimeter to several millimeters. |
Manufacturing | Primarily produced through hot rolling as individual plates or cut from thick coils. | Produced through hot or cold rolling and then coiled. |
Handling & Transport | Transported as flat stacks, requiring careful handling to prevent bending. | Transported as coils, which are more compact for a given length of steel. |
Production Efficiency | Less suited for high-volume, automated production lines. | Ideal for continuous, high-speed manufacturing processes. |
Primary Advantage | Superior strength and structural integrity due to its thickness. | Efficiency in fabrication, leading to lower processing costs in high-volume applications. |
Common Surface Finish | Often has a rougher, “scaly” finish if only hot-rolled. | Can have a hot-rolled finish or a smoother, more refined cold-rolled finish. |
Typical Applications | Structural components for buildings and bridges, shipbuilding, heavy machinery, pressure vessels, and industrial equipment. | Automotive bodies and parts, appliances (refrigerators, washing machines), roofing, ductwork, and furniture. |
Phần kết luận
Understanding the basics of steel plates and coils is crucial for selecting the right material for your project. Each type offers unique properties that make it suitable for specific applications. By choosing the appropriate steel product, you ensure durability, efficiency, and cost-effectiveness in your work.
Câu hỏi thường gặp
What is the difference between hot-rolled and cold-rolled steel?
Hot-rolled steel is processed at high temperatures, resulting in a rough surface finish and looser tolerances. Cold-rolled steel is processed at room temperature, offering a smoother finish and tighter tolerances.
Why is galvanized steel used for outdoor applications?
Galvanized steel has a zinc coating that protects it from corrosion, making it ideal for outdoor use.
Can stainless steel rust?
While stainless steel is highly resistant to corrosion, it can rust under extreme conditions or if the protective chromium layer is damaged.
What factors should I consider when choosing steel for a project?
Consider the required strength, corrosion resistance, surface finish, and cost.
Is cold-rolled steel more expensive than hot-rolled steel?
Yes, due to the additional processing, cold-rolled steel is generally more expensive than hot-rolled steel.