Welcome to My Blog!
Before we dive into the content, I’d love for you to join me on my social media platforms where I share more insights, engage with the community, and post updates. Here’s how you can connect with me:
Facebook:https://www.facebook.com/profile.php?id=61571539990739
Now, let’s get started on our journey together. I hope you find the content here insightful, engaging, and valuable.
جدول المحتويات
مقدمة
When you’re working with steel—whether forging, welding, casting, or heat-treating—knowing the melting temperature of steel is absolutely essential. Why? That exact threshold determines everything from material strength and durability to processing efficiency and product performance. Understanding what melts, when and how is the foundation of safe and effective steel use across industries.
In this blog, we’ll explore the basics and nuances behind steel’s melting behavior, explore how alloys shift those numbers, unpack why it matters for your manufacturing or fabrication, and answer all your questions. You’ll get expert tips, real-world insights, and solid data that highlight how this single property influences project outcomes every time.
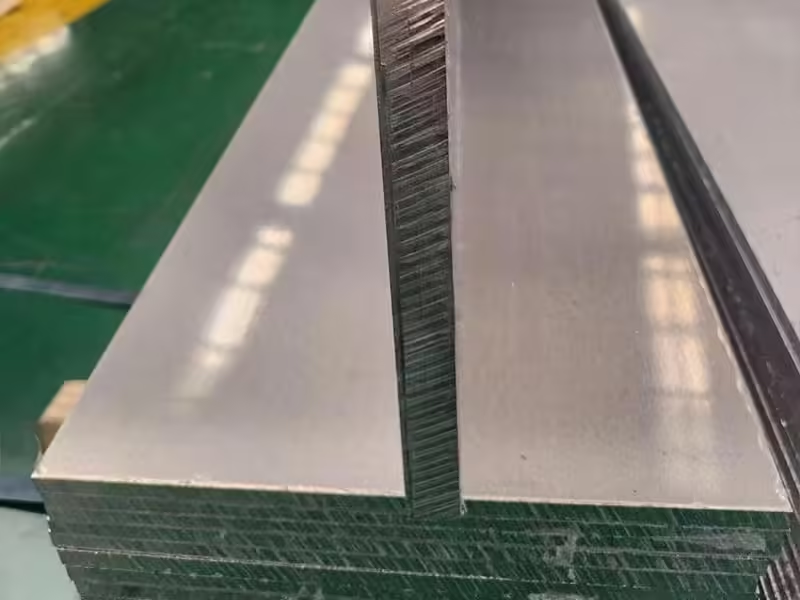
What Is the Melting Temperature of Steel?
Basics of Pure Iron vs. Steel
Steel is primarily iron with carbon and other elements. Pure iron melts at approximately 1538 °C (2800 °F). When you add carbon or alloying elements, the melting point drops—or occasionally rises—depending on composition. So when discussing melting temperature of steel, you’re usually referring to ranges rather than fixed points.
Typical Melting Ranges for Common Steels
Steel Type | Composition | Melting Range (°C) |
---|---|---|
Carbon Steel (low alloy) | ≤0.3% C | 1450–1520 |
Medium Alloy Steel | 0.3–0.6% C + Mn, Si, Cr, Ni | 1400–1510 |
High Carbon / Tool Steel | ≥0.6% C + W, Mo, V | 1300–1450 |
Stainless Steel (304/316) | 17–19% Cr, Ni + C, Mn | 1400–1450 |
These numbers are confirmed by ASM International metallurgical tables and support real-world processes in casting, welding, and forging.
Why Melting Temperature of Steel Is Critical in Applications
Forging and Casting Success
In forging, heating steel to just below or slightly above its melting point makes it ductile enough to shape. Heating too little results in cracks and poor flow; too much—especially above the melting temperature—leads to surface breakdown, scale, or unwanted slag.
For casting, knowing the melting range ensures your steel alloy solidifies with proper grain structure and minimal porosity, which is essential for structural components like machine housings or crankshafts.
Welding Integrity and Strong Joints
In welding, molten zones form during fusion. Understanding the melting temperature helps you control heat-affected zones and prevent unwanted melting or metallurgical degradation. For example, welding high-carbon tools requires precise preheat and interpass temperatures to avoid cracking.
Heat Treatment Processes
Processes like annealing, tempering, and quenching depend heavily on knowing melting temperature to define critical points—like A1 (727 °C) and A3 (912 °C) for carbon steels. This lets you control phase transformations (austenite, martensite, etc.) that define hardness or toughness in the final product.
Factors That Shift the Melting Temperature of Steel
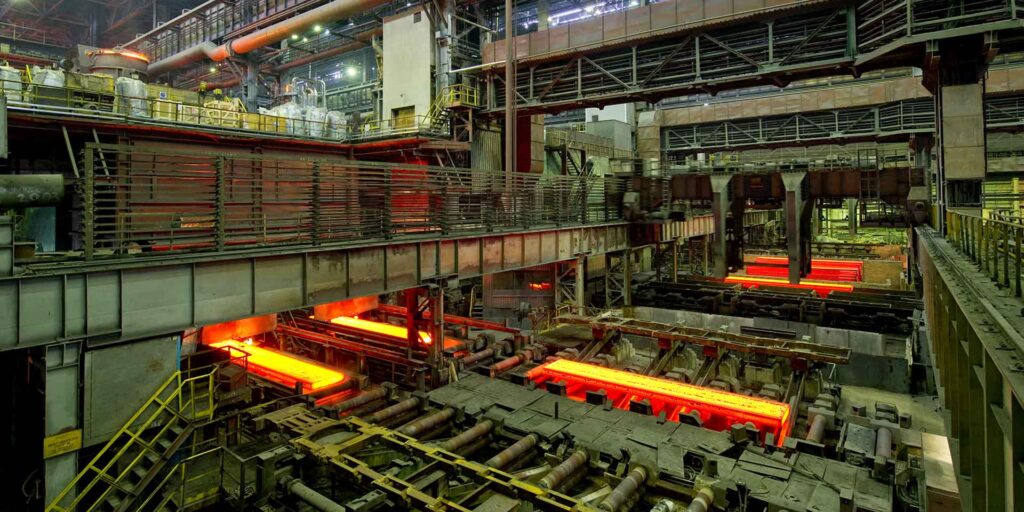
Carbon Content Influence
More carbon lowers the melting point. High-carbon tool steels may start melting in the lower range of 1300 °C. This affects how steel responds to thermal processes and whether certain alloys are suitable for extreme applications.
Alloying Elements
Chromium, Molybdenum, Tungsten, Vanadium – These can either raise or lower melting points depending on interaction
Nickel and Manganese – Often lower melting ranges but also increase toughness and corrosion resistance
Silicon – Helps deoxidize and lowers melting slightly
Impurities and Inclusions
Trace elements like sulfur, phosphorus, or oxygen can form low-melting-point compounds that cause hot-shortness—brittle failure at high temperatures.
Heat Treatment and Microstructure
The steel’s microstructure—ferrite, pearlite, martensite—determines mechanical strength and the solidification behaviors near melting. That’s why mill data sheets and phase diagrams play a crucial role during processing.
Real‑World Scenarios: Where Melting Temperature of Steel Matters Most
Industrial Foundries and Casting
In casting gears, pump housings, or valve bodies, pouring steel at the right temperature (above liquidus but under turbulence) is vital. Keeping the alloy temperature within 10–20 °C above melting range improves mold filling and reduces porosity.
Automotive Welding and Manufacturing Plants
Automobile assembly uses robotic welding on steel frames that require precise heat control to maintain structural integrity and dimensional stability. Suppliers aim to avoid distortion and hot cracks.
Construction and Heavy Fabrication
Structures like bridges or cranes rely on welded and forged connections. Heat treatments that don’t respect melting thresholds could lead to failure under load—especially in cyclic or environmental stress conditions.
Tool and Die Making
Tool steels operate near their melting points during forging and heat-treating. Exceeding that can cause grain coarsening, crack initiation, or loss of toughness—disastrous for tooling that demands long cycle lives.
How Engineers Measure and Use Melting Temperature Data
Differential Scanning Calorimetry (DSC)
DSC precisely identifies when steel transitions from solid to liquid. It provides phase-transition details that are essential for low-alloy or specialty steels used in high-temperature applications like aerospace.
Thermodynamic Modeling
Software tools that calculate phase diagrams (e.g., Thermo‑Calc, JMatPro) simulate melting and solidification behavior based on complex compositions—helping engineers design new alloys or refine heat-processing windows.
Accredited Industry Standards
Organizations like ASM International, SAE International, and ISO publish tables of melting data. Manufacturers quote alloy melting ranges as standard specs, which fabricators rely on.
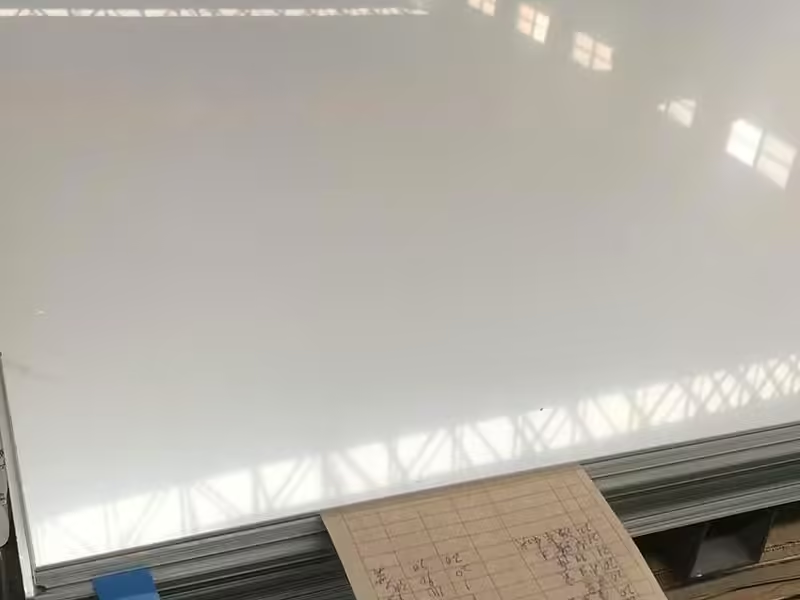
Tips for Working With Melting Temperature in Practice
Always refer to the mill’s certified data sheet for the exact alloy you’re using
Allow margins: heat just 10–20 °C above the solidus—more in casting, less in forging—to avoid overheating
Use inert or reducing atmospheres during high‑temp heating to prevent scale and oxidation
Cool steel slowly past melting thresholds to avoid stress cracks or embrittlement
خاتمة
Understanding the melting temperature of steel ties directly into every stage of metalworking—from forging clean flash pieces to welding durable structures and heat-treating high-performance tools. It underpins safety, quality, efficiency, and predictability in industrial processes.
If you’re working with steels in welding, casting, toolmaking, or manufacturing—and want tailored insights or help optimizing temperature profiles—our metallurgical experts are ready to support you.
📩 Contact us today to discuss your materials, processes, and how to get the heat right every time.
الأسئلة الشائعة
Why does melting temperature of steel vary so much?
Because alloy composition, carbon content, and microstructure all shift melting behavior—so it’s a range, not a point.
Can you weld any steel if you know the melting range?
Knowing it helps you set parameters, but weldability also depends on carbon equivalent, thickness, and heat input control.
Does melting temperature affect strength?
Yes, heating above critical temperatures changes steel’s structure—and reheating beyond melting can degrade properties permanently.
How precise do I need to be?
±10 °C is usually fine for casting or forging—but micro-alloy work might demand ±5 °C, requiring advanced thermal control.
What happens if you weld near the melting point?
You risk burn-through, grain coarsening, or HAZ brittleness. Stay below that threshold for safety.