What is coiled metal and how is it used? This blog tells you the answer!
Before we dive into the content, I’d love for you to join me on my social media platforms where I share more insights, engage with the community, and post updates. Here’s how you can connect with me:
Facebook:https://www.facebook.com/profile.php?id=61571539990739
Now, let’s get started on our journey together. I hope you find the content here insightful, engaging, and valuable.
جدول المحتويات
مقدمة
Coiled metal refers to metal sheets that have been rolled into continuous coils, a form that facilitates efficient storage, transportation, and processing. This format is prevalent in various industries due to its versatility and ease of handling. Coiled metal is produced through processes like hot rolling or cold rolling, depending on the desired properties and applications.
What Exactly Is Coiled Metal?
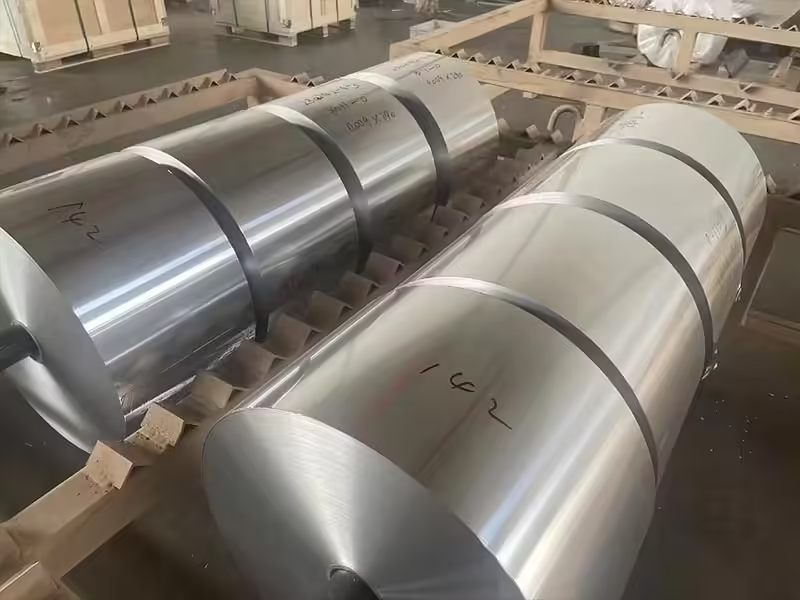
Defining Coil Metal
Coiled metal refers to long, continuous strips of metal—typically steel, aluminum, copper, or alloys—that are wound into tight, cylindrical rolls for easy storage, transport, and processing. These coils are produced by rolling metal sheets or strips through specialized machines, creating a compact form that’s ideal for high-volume manufacturing.
According to a 2023 report by the World Steel Association, over 50% of global steel production is processed into coils due to their efficiency in handling and versatility in applications.
How Metal Coils Are Made
The journey of coiled metal starts in a mill, where raw metal is heated, rolled, and shaped. Here’s a quick rundown of the process:
- Hot Rolling: Metal is heated to high temperatures and passed through rollers to reduce thickness and form long strips.
- Cold Rolling: For smoother surfaces and tighter tolerances, the metal is further rolled at room temperature.
- Coiling: The finished strip is wound into a coil, often weighing several tons, for easy handling and shipping.
- Surface Treatment: Coils may be coated (e.g., galvanized or painted) to enhance durability or corrosion resistance.
This process has been continuously refined over decades, ensuring that coiled metal meets stringent quality standards, making it a reliable choice for manufacturers around the world.
Why Coiled Metal Is a Manufacturing Staple
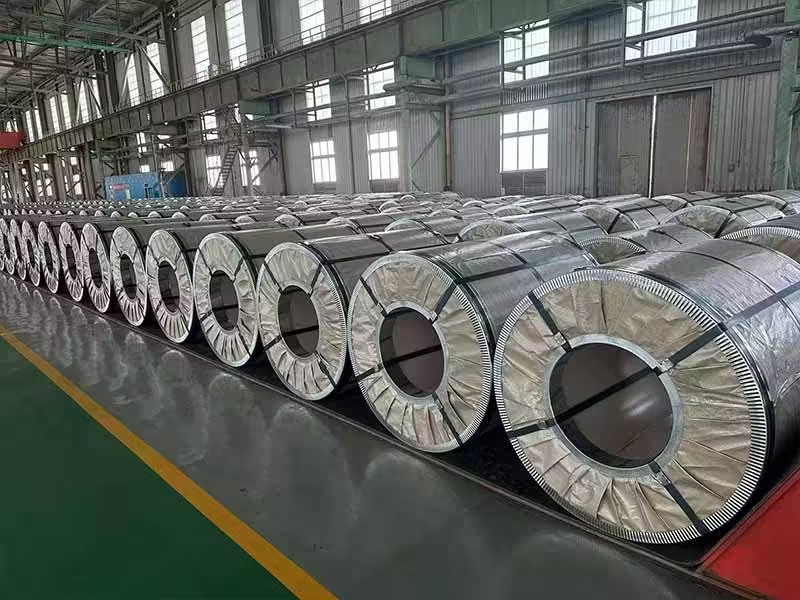
Efficiency and Cost Savings with Metal Coils
Efficiency is a top priority in plant operations. Coiled metal shines here because of its continuous form, which allows it to be fed seamlessly into the production line. Unlike flat metal, which requires frequent loading and unloading, coils can be unwound and processed without downtime. A 2024 Manufacturing Institute study found that using coiled metal can reduce material handling time by up to 35% in the automotive and appliance manufacturing industries.
For you, this means faster production cycles and lower labor costs. Plus, the compact nature of coils saves storage space, allowing you to store more material without cluttering your facility. It’s a win-win for maintaining a lean and efficient operation.
Versatility Across Industries
One of the biggest advantages of metal coils is their adaptability. They are used in a wide range of industries, including automotive, construction, electronics, and packaging. For example, steel coils are used to make car bodies and structural beams, while aluminum coils are key to lightweight aerospace components and beverage cans. Copper coils, on the other hand, are essential for wires and transformers. This versatility makes metal coils a material of choice for manufacturers, helping them meet diverse needs without changing suppliers or processes.
Enhancing Precision and Quality
In modern manufacturing, precision is critical, and metal coils provide just that. The rolling process ensures uniformity in thickness and width, which ensures consistent quality in the final product. Whether you are stamping parts or forming complex components, metal coils minimize defects and waste.
Common Types and Applications of Metal Coils
To help you understand the various coil options and their uses, here is a detailed table listing the most common types, their characteristics, and their advantages in the industry.
Type of Coiled Metal | Key Properties | التطبيقات الشائعة |
---|---|---|
Steel Coiled Metal | High strength, durable, available in hot-rolled or cold-rolled forms | Automotive (car bodies, chassis), construction (beams, roofing) |
Aluminum Coiled Metal | Lightweight, corrosion-resistant, highly formable | Aerospace (aircraft panels), packaging (cans, foil) |
Copper Coiled Metal | Excellent conductivity, malleable, corrosion-resistant | Electronics (wiring, circuit boards), HVAC systems |
Stainless Steel Coiled Metal | Corrosion-resistant, hygienic, aesthetically pleasing | Medical equipment, kitchen appliances, architectural panels |
Alloy Coiled Metal | Customized properties (e.g., strength, heat resistance) | Specialized industrial components, energy sector (turbines) |
Possible Challenges and Considerations
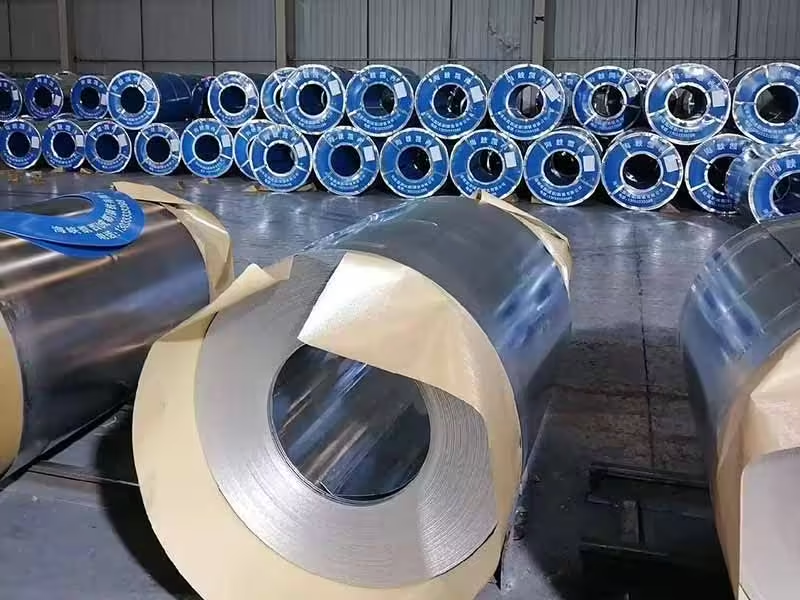
Handling and Storage of Coiled Metal
Although metal coils are compact, they can weigh several tons and require specialized equipment such as forklifts or cranes to move. Improper storage practices, such as exposing coils to moisture, can lead to corrosion, especially on untreated steel. To avoid this, you need to store coils in a dry, controlled environment and follow proper handling protocols.
Processing and Equipment Requirements
Handling coiled metal requires the right equipment. For example, you need an uncoiler to unwind the metal and feed it into the production line. If you are cutting or forming the coil, precision tools such as slitters or punches are essential. While these investments can be large, the savings in efficiency and material usage in the long run usually outweigh the initial cost.
خاتمة
Coiled metal plays a crucial role in modern manufacturing and construction. Its various forms and properties allow it to meet the diverse needs of multiple industries. Understanding the types and applications of coiled metal can aid in selecting the appropriate material for specific projects, ensuring efficiency and durability.
الأسئلة الشائعة
How does coiled metal differ from flat metal?
Metal coils are rolled into continuous coils, making them easier to store, transport and feed into automated production lines. Flat sheets, while versatile, require more manual work and take up more space.
What are the main types of coiled metal?
The main types include hot-rolled, cold-rolled, galvanized and pre-coated coil metal, each with specific properties and uses.
How do I prevent coiled metal from corroding?
Store coils in a dry, temperature-controlled environment and consider using treated coils (such as galvanized or coated coils) to enhance corrosion resistance. Protective packaging during transportation can also help improve corrosion resistance.
What industries rely most on coiled metal?
Automotive, construction, electronics, aerospace and packaging are major users, but the versatility of coils makes them valuable in many fields.
How do I choose the right type of coiled metal for my project?
Consider the project requirements – strength, weight, corrosion resistance or conductivity. You can consult with metal supplier-Huanhaizhongke to find the material and treatment method that best meets your needs.